What do milk foam and cleaning products have in common?
PCV Group: Developing new packaging solutions through Cross Innovation
Sustainable, environmentally friendly, sturdy and hygienic: packaging materials have to meet ever-more-demanding requirements, especially when they contain consumer products. For this reason, manufacturers are searching for new materials, while also enlarging existing packaging designs. “For example, in the cleaning products sector, the concentrations of the chemical constituents are being increased, so that a single package lasts the customer longer,” relates Martijn Torenbeek of the PCV Group. In this contribution, the engineer from the company based in Enschede, the Netherlands, describes the role that cross innovation plays in the development of new packaging solutions.
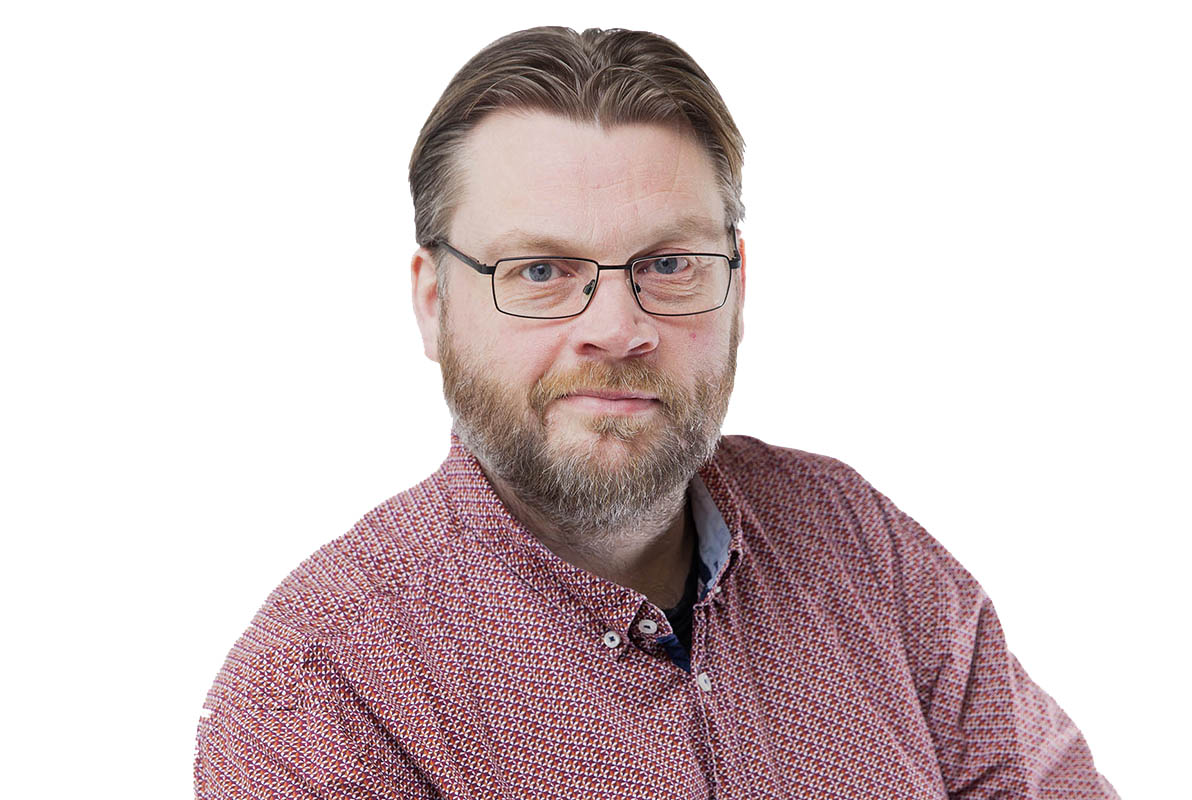
One environmental policy objective is to reduce packaging waste. Many companies achieve this by offering more concentrated versions of their products – in particular, detergents and cleaning products. “For example, our customer Dr. Weigert makes liquid dishwasher detergents, among other products. The challenge was to find the right ratio for the mixture of the highly concentrated chemicals and the associated water in the new package. At the same time, we had to ensure the safety of consumers so that, for example, the liquid wouldn’t squirt into people’s eyes. On top of that, the plastic the packaging was made from had to be able to resist the increased concentration”, Martijn Torenbeek explains.
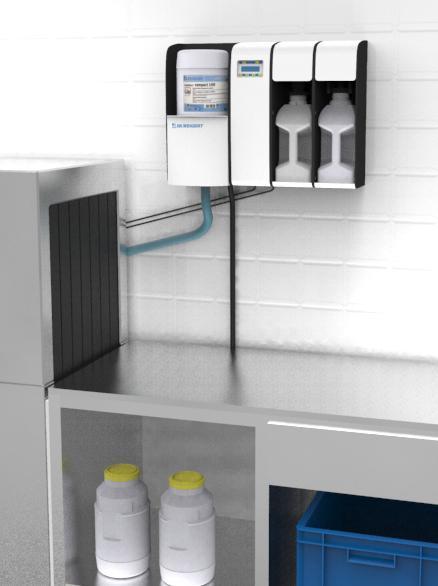
A common basic principle
This was one task where the PCV Group could apply its Cross Innovation approach. “We went back to our expertise with mixtures of milk, air and steam in milk foaming systems for coffee machines. Whether you’re mixing a chemical detergent with water, or milk with steam, the basic principle here is exactly the same. You have to take the same aspects into account”, Torenbeek emphasises.
The solution: “We have developed an intelligent interface between the bottle and the dishwasher, which safely transfers the cleaning product into the appliance, whether the concentrate is in liquid or granulated form. We also made sure that the consumer won’t come into direct contact with the concentrated chemical ingredients, so their skin and eyes are protected.”
The dishwasher also uses a peristaltic pump, like the ones found in high-end coffee machines, to empty the packaging. “The pump consists of a hose which – in simple terms – is squeezed at certain points, causing the media to flow. This is a very common technology”, the engineer explains. In both the dishwasher and the coffee machine, the media being pumped shouldn’t come in contact with the pump itself. Although the reasons are very different in the two cases, the principle is exactly the same. In this way, the PCV Group has succeeded in enabling precise dosing, while ensuring the necessary safety of the consumer.
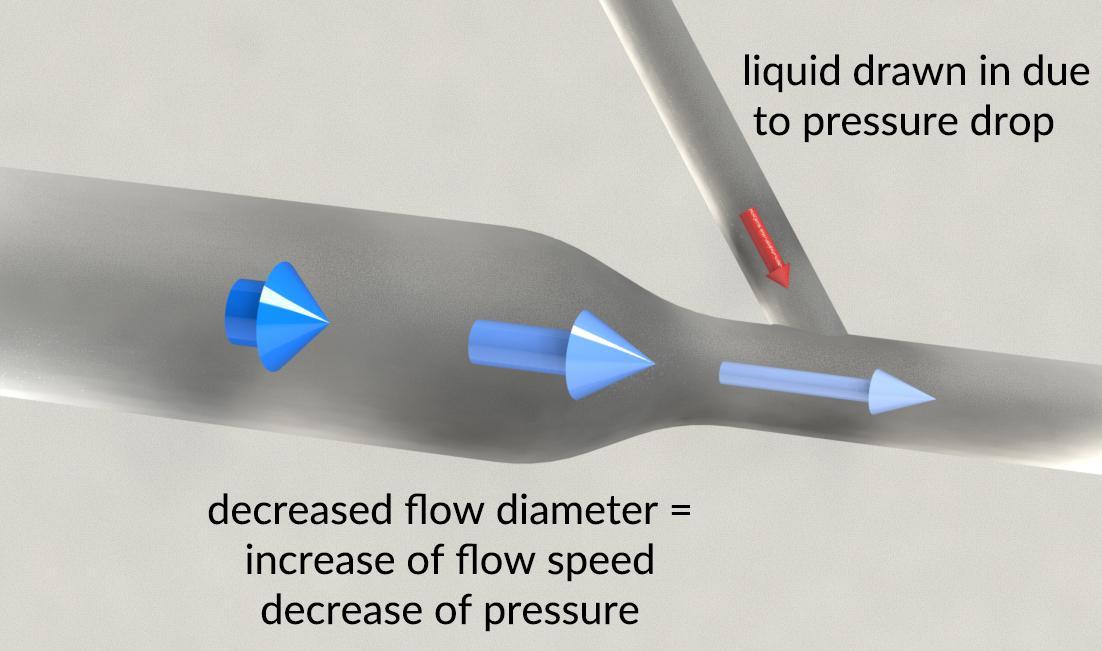
The PCV Group has a lot of experience with such solutions, and especially with Venturi systems, so can quickly calculate the relevant flow data, while at the same time taking advantage of simulation software and many years of testing experience.
“We also work for several customers in the chemical industry on dosing systems for concentrated chemicals. The big challenge there is also to mix the chemical with water in the right ratio, and under an extreme range of conditions in terms of fluidity, pressure, viscosity, and temperature. This calls for complex measurement and control systems on the one hand, and on the other, simpler systems based on the Venturi effect. In turn, this requires a great deal of experience in fluid mechanics and Venturi geometries. And that is what we provide.”
New materials
In recent years, the engineers of the PCV Group have developed their expertise in the packaging area – and also applied the cross innovation approach here. “In this case, cross innovation refers to the method used: we have taken the same approach as we have done in completely different industries. For example, when we are developing technical concepts, we follow a structured and efficient approach. We have defined processes and a wide variety of tools that we can employ. It was exactly these methods that we applied when developing a new type of packaging for an espresso machine manufacturer”, Torenbeek recalls.
An alternative to expanded polystyrene
When it comes to packaging material for electrical devices, expanded polystyrene is usually the first choice, albeit not a particularly environmentally friendly one. For this reason, a well-known manufacturer of espresso machines commissioned the PCV Group to find an alternative to expanded polystyrene. The material had to be just as versatile in terms of how it could be shaped, and be at least as drop-proof as expanded polystyrene. It also had to give the customer the feeling of having a high-quality product in their hands as they unpacked it. One other requirement: as the appliances are packed in Romania, the required materials also had to be available there.
Based on these requirements and tried-and-tested internal procedures, the engineers developed a project plan. This started with the search for a suitable material. “We reviewed the market and systematically evaluated the available options, from paper to plastics. After a first analysis, we had a short-list of 20 materials”, recalls Martijn Torenbeek.
In the second step, the necessary drop testing was carried out with the help of a network partner in Italy. “We benefited from our partner’s expertise in simulation tests. The combination of simulation and practical drop testing accelerated the optimisation process considerably. Better results could therefore be obtained in a shorter time. We developed and modified the design according to the relevant test results. Our focus was on the behaviour of the packaging itself and how the espresso machine was affected; in particular, the G-forces acting on the packaging were important. Was there any cracking or deformation? Based on these tests, a few materials could be rejected at this stage.” Finally, practical tests were conducted with the candidate materials. Eventually, a modern corrugated paper board was selected, meeting all the customer’s requirements: from durability to recyclability, from its availability in Romania to its high-quality look and feel. “Here too the source of our success was not so much our expertise in another field, but the structured approach that has become part of our DNA in other sectors.”
Films
Incidentally, the next assignment in the packaging field is already waiting: up to now, a wide range of products have been shrink-wrapped in films. However, these films are difficult or impossible to recycle, and so should be gradually withdrawn from the market. The challenge with these films is that they consist of different layers (multi-layered), each of which fulfils a different function. Now a single material must be found with all these properties, while also being reusable. A tough problem, and one that the experts at the PCV Group are also working on. Another job for cross innovation...